瞭解 CIP 優化在實現釀造質量和可持續性方面的關鍵作用。
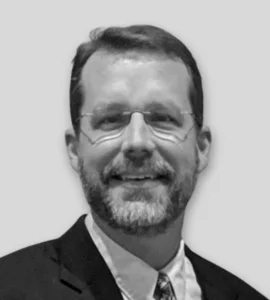
作者:Andrew Klosinski,高級生產工藝工程師
釀酒行業正在經歷來自各個方向的重大變化。啤酒廠正在應對因退休和人員流動而導致釀造的知識庫的匱乏,面臨招聘新進人員挑戰並以精簡的人員配置維持運營。這限制了釀造人員完成要求他們完成的所有工作的時間。因此,對原位清洗 (CIP) 系統的瞭解較少,也很少有時間查找有關生產設備的老化和老舊的設施圖紙的文檔。此外,對績效指標的審查越來越嚴格,對可持續性的關注也越來越高。儘管存在這些挑戰,但仍存在優化的機會,而 CIP 是啤酒廠獲得許多好處的關鍵。讓我們開始吧……
高效釀造是一種平衡行為
作為釀酒商,我們利用我們的創造力和技能為顧客生產最好、最有吸引力的產品。簡而言之,我們釀造——或者這就是外界認為我們做的事情。實際上,我們的大部分時間都花在了在這個充滿挑戰的行業中取得成功所需的無數活動上:生產調度、設備維護和材料採購以及與人員相關的專案,例如人員配備、安全和培訓。有些日子,我們幾乎只能將啤酒送到客戶手中。
然後,在這一切之後,我們將剩餘的注意力和資源轉向清潔和衛生。
釀造成功建立在清潔和衛生的基礎上
我們的消費者可能沒有考慮過,但作為釀酒商,我們的成功建立在我們的清潔和衛生能力和實踐的基礎上。由於衛生是釀造的一個基本方面,它應該並要求與我們投入大量精力和熱情的如同成分及配方一樣重要。想一想您的啤酒廠。CIP 在知識、理解和關注的層次結構中處於什麼位置?他們是:
- 做得好嗎?
- 重複?
- 以正確的頻率執行?
- 以可持續的方式完成?
- 事後的想法還是僅僅完成的任務?
讓 CIP 不僅僅是一個複選框練習:清潔的本質
想像一下,將 CIP 超越「勾選框」練習會是什麼樣子。考慮一下您的產品的好處。考慮通過降低水、化學、下水道或廢水成本來提高您的獲利能力。想想這如何在您的員工培養技能、學習釀酒的關鍵要素併為之感到自豪時,在參與度和授權方面受益。
將您的方法和理念提升為始終如一地執行高品質的 CIP 是觸手可及的,並且會帶來回報。
從這時起,我們將“用心清潔”,並且與任何旅程一樣,我們將從頭開始。Clean with Intent 要求我們全面了解系統硬體、檢測和控件。它由 Change Management 指導、支持和基礎。每個步驟都遵循 Inquire、Observe、Document、Verify 和 Implement 的路徑,如圖 1 所示。
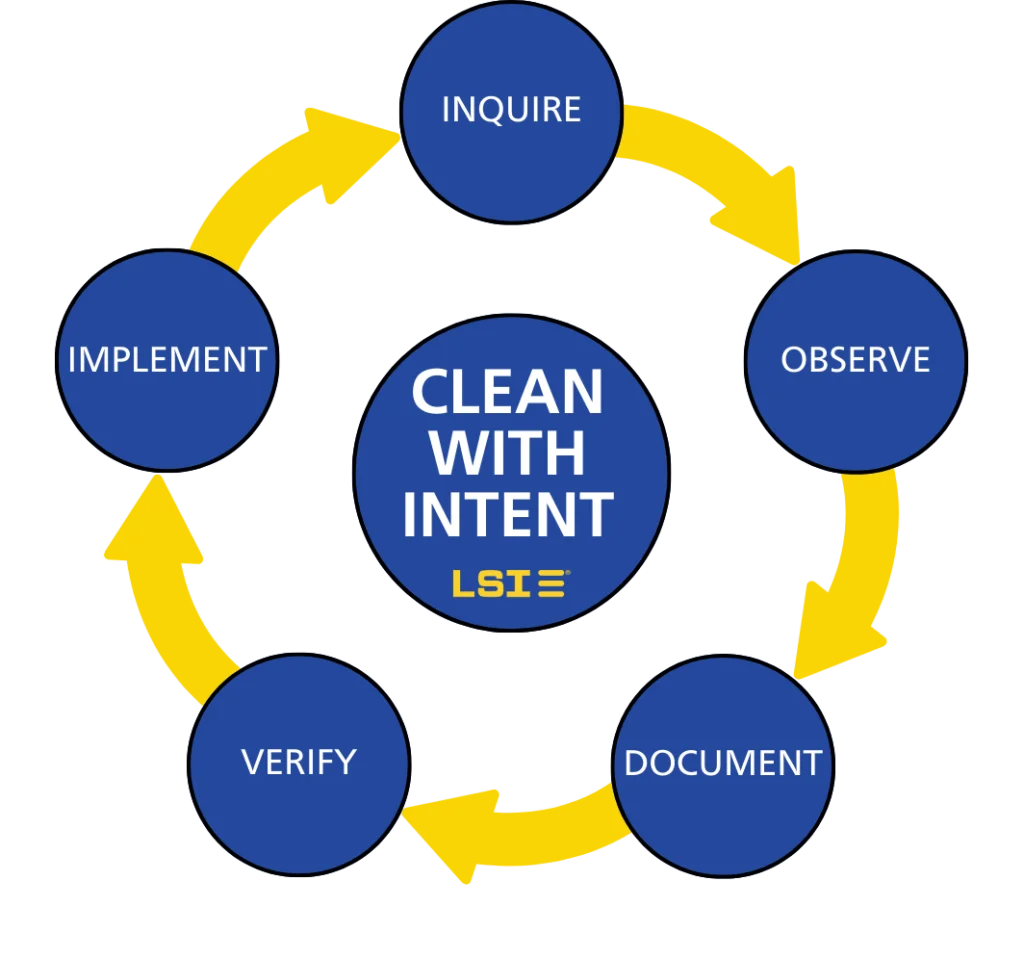
通過三個問題構建 CIP 知識
學習始於好奇心。 我們通過提出三個問題來構建我們對 CIP 的瞭解:
- CIP 的目的是什麼?
- 該系統是否能夠滿足這些要求?
- 當前採用的技術是否適合該應用?
在許多情況下,第一個問題 – CIP 的意圖 – 可能是一個簡單明瞭的對話。對於大多數人來說,CIP 旨在為釀造、發酵、運輸、過濾、儲存或包裝產品提供清潔衛生的環境。“clean” 和 “sanitary” 的確切定義可能是大多數討論的重點。花上所需的時間,並召集一個具有廣泛知識基礎的團隊,以明確設定這些期望,並圍繞“清潔”和“衛生”建立規範。能夠量化、測量、比較和趨勢化 CIP 數據是成功的關鍵。
一旦圍繞 CIP 的意圖創建了結構,確定其當前狀態功能可能會牽涉許多關鍵問題,並且可能會導致需要做一些功課。 對於我們中的許多人來說,我們繼承了我們工廠的系統。最初的設計和生產工藝流程可能已經改變和擴展。老化的生產設施、不同的維護水平和不斷增加的設備成本可能導致原來的 CIP 系統在今天看起來與最初調試時大不相同。示例問題可能類似於:CIP 供料泵葉輪的直徑是多少?那個 CSS 泵以前是否以固定速度運行? VFD 是什麼時候添加的?您知道每個容器中的清潔機構類型嗎? 每台清洗機的噴嘴直徑是否相同?等等。
我們的流程是否與不斷發展的啤酒行業保持同步?
隨著啤酒廠產品群組擴展到不同的新型飲料,請考慮一下這對我們的CIP系統的影響。例如,曾經專為啤酒生產設計的 CIP 系統是否能夠解決和消除不同的生產批次之間的風味殘留?當前的儲存槽清潔機制是否能夠去除酵母菌株、非麥芽麥芽汁或不斷變化的生產原料中的固體和殘留物?
使用生產工藝流程圖獲取CIP 工藝細節
如您所見,可能有許多未知數需要解決。這就是流程圖 (PFD) 提供起點的地方,以説明這項工作並指明學習的流程細節(參見圖 2 中的範例)。CIP 通常通過環路或電路進行,而不是一次性進行。有了這個,從清潔液槽開始,然後逐步完成迴路,識別並記錄每個泵、電機、閥門、儀器、熱交換器、化學物添加點、清潔機和容器的詳細資訊。其中一些工作可以利用現有的流程和儀錶圖 (P&ID)、通過計算機化維護管理系統 (CMMS) 獲得的資訊和設備手冊來完成。這些有價值的資訊反映了 CIP 循環的當前狀態,並引導我們進行下一步 – 驗證。
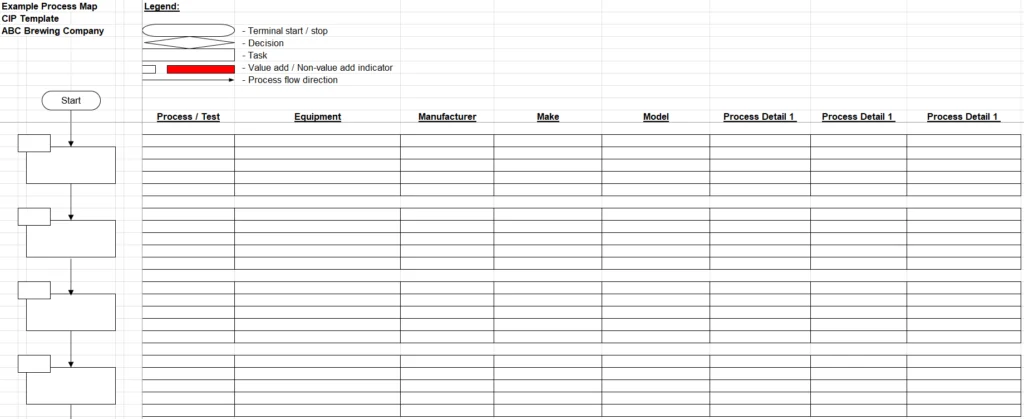
到現場去驗證!
正是在這一點上,我們利用對製造生產過程的理解並物理驗證其細節——品牌、型號、尺寸、馬力、直徑、測量範圍等。 這是一項實地考察工作,在依循該過程時需要攀爬、爬行。 在此過程中,您將獲取銘牌和其他重要細節,以便與原始 PFD 進行比較。 您在現場找到的資訊可能並不總是與過去的文件一致。 這沒關係,這就是這項工作的重點:我們需要瞭解當今存在的系統組成部分。 有了完整的當前狀態的流程資訊,我們現在可以繼續回答這個問題 – CIP 系統是否能夠滿足所要求的需求和可達成預期的成果?
清潔的四個基本要素
在審查了 PFD 中記錄的細節后,我們現在可以根據清潔的四個基本原則——時間、作用、化學和溫度(TACT-圖 3)確定實現我們對清潔和衛生定義的能力。
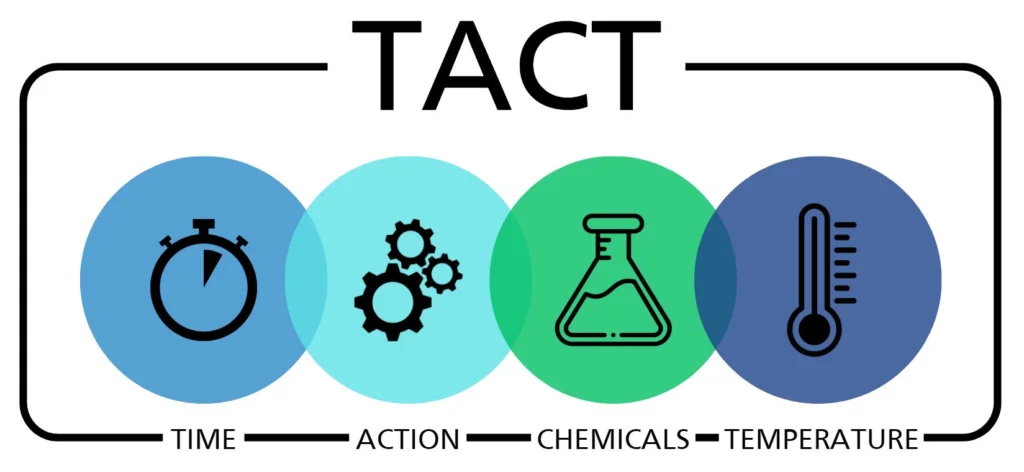
濃度 – 溫度和化學成分
對於溫度和化學 (類型和濃度) 的 CIP 原則,我們必須考慮我們在清潔過程中要解決的問題 – 例如固體、香料、薄膜和泡沫。 在這一點上,沒有比與您的清潔化學品供應商合作更好了。 他們擁有資源和專業能力,可以推薦和採購特定適合於您的應用的清潔劑。 自行執行此工作可能會浪費資源(化學品、水、工作力),可能會造成不必要的設備受到損壞,並且可能不安全。
在我釀造生涯的早期,有人問我:“你能找到的最好的工具是什麼? 思考片刻之後,我的腦海裡浮現出了學校期間積累的許多參考書。 我提出這個作為我的答案。 “好主意,”他回答道。 “不過,你手頭最好的工具就是這個,”他指著電話。 “有了這個,您只需致電專家即可獲得有關任何主題的幫助和知識。” 簡單、強大,而且非常正確。
請聯繫您的化學品供應商代表,利用您擁有的和已經通過購買化學品供應商以取得最佳的的資源。
獲得這項支援后,您將獲得有關溫度和濃度目標的指標。 然後,我們可以返回到 PFD 詳細資訊並檢查我們的系統功能。 它能達到推薦的溫度嗎? 化學品如何計量、均質化、流通和驗證? 最重要的是,這些可以安全地完成嗎?
一旦證明其能力,我們就會通過測量清洗液的溫度和濃度來驗證它。 理想情況下,這是通過在線檢測來實現的。 如果不可行,手動測量同樣有價值;它們只需要對數據進行更多的驗證、勞動和調整處理。 無論使用哪種方法,文檔都是一種重要的並且能驗證的成果。
“通過記錄工藝條件和結果,您可以清楚地記錄當前生產工藝,並為子孫後代提供路線圖。”
通過這些努力,我們現在已經實現了最佳溫度和濃度。 然而,仍可能產生不合格的 CIP。 我們必須平等地對待所有清潔原則。 為此,我們將注意力轉向清潔作 – 提供出色 CIP 的機制。
通過這些努力,我們現在已經實現了最佳溫度和濃度。 然而,仍可能產生不合格的 CIP。 我們必須平等地對待所有清潔原則。 為此,我們將注意力轉向清潔作 – 提供出色 CIP 的機制。
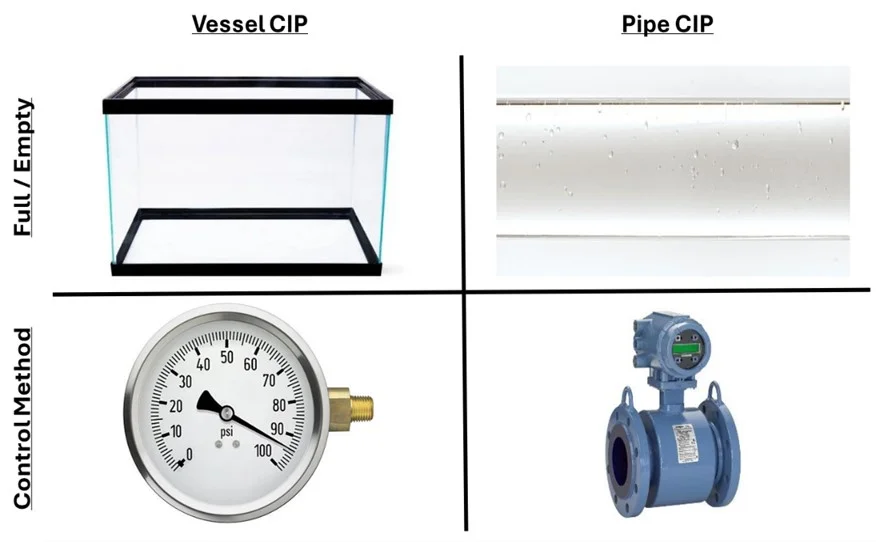
時間 – 它比你想像的更重要
實現理想的 CIP 還需要什麼? 時間。 清潔的第四個方面,也許也是最不被理解的方面。 準確瞭解清潔、沖洗和消毒儲罐和管道需要多長時間,可以將CIP 從曾經可能“只是另一項工作”提升為可以提高產品品質、增強可持續性足跡並節省化學品和勞動力費用的工作。 好的,聽起來很神奇 – 我們如何為 CIP 的每個元素確定處理時間? 讓我們來看看。
對於配備清洗機的容器,供應商會提供有關供應壓力、RPM 和完成一個完整清洗儲存槽的週期所需的轉數的詳細資訊。 通常,較高的清洗液供應壓力會導致 RPM 增加,並有可能在更短的時間內進行儲存槽清洗。
在下面的圖 5 中,您可以看到如何實現完整的清潔週期。 請注意,即使使用一種模式,整個儲存槽也已暴露在清潔溶液中。每個後續模式繼續填充最初不受清潔噴嘴影響的空間。 瞭解迴路和模式如何協同工作是節省時間和水的重要手段,尤其是在預沖洗、最終沖洗和衛生過程中。在這三種情況下,沒有必要對容器的每一平方英寸進行直接噴射衝擊,因為只需分配、潤濕容器表面和級聯清潔溶液就足夠了。 只有在鹼液清洗期間,才需要一個完整的周期來確保容器的完全清潔。
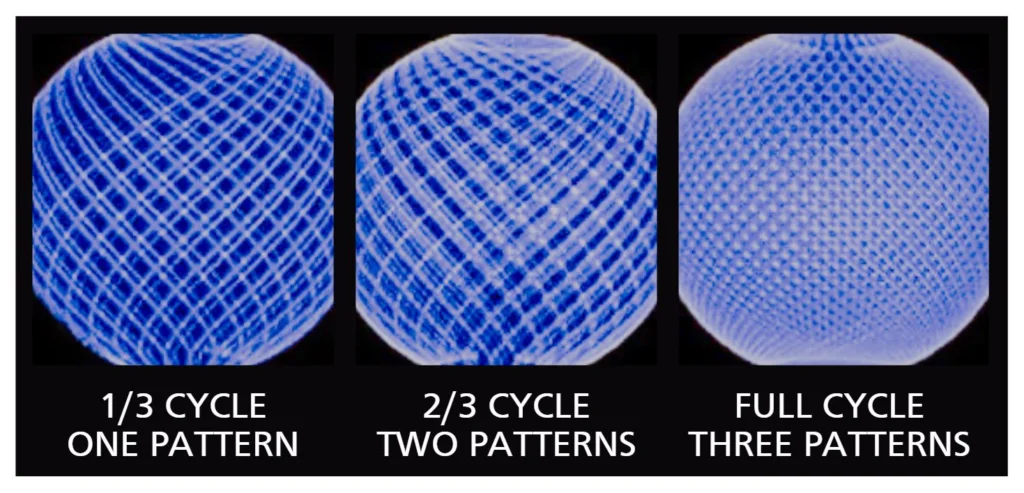
計算周期時間
是時候(是的,我剛剛說了)進行快速練習。 讓我們計算發酵罐的鹼液循環總時間。 從清潔機手冊中,我們確定完成一個週期需要 45 轉。 在我們的 125 PSI 供應壓力下,我們的清潔機以 5 RPM 的速度旋轉。 以下是週期時間的方程式:
在此示例中,週期時間為9分鐘。 供應鹼液的時間少於此時間可能會導致清潔不徹底。 在苛性鹼中花費的時間超出我們的計算值將產生遞減的回報,並可能使您失去生產可用性。
從我們剛才討論的內容來看,使用工藝用水進行鹼液后沖洗的合適循環時間是多少? 一次漂洗需要多少個循環? 考慮一下漂洗的目的。 在這樣的步驟中,我們希望去除所有的鹼液,並將水箱恢復到中性 pH 值。 有了這個,如果你說只需要一種模式,那你就走在正確的軌道上。 運行淡水沖洗 3 分鐘是一個很好的起點,可以通過在線監測或對沖洗水 pH 值進行樣品測試進行驗證,以確保完全沖洗。
除了時間的影響之外,還可以考慮一下您可以節省的用水量。 瞭解您的 CIP 系統設備的詳細資訊將導致各種形式的節省。
對於噴霧球,我們將採取不同的方法。 噴淋球和噴管在 CIP 時間方面有很多共同點。 在這兩種情況下,我們都需要以「價格合適」的方式執行每個清潔步驟 – 只要有必要,就不要超過。 幸運的是,有一些儀器和工具可以讓我們深入瞭解我們正在進行的清潔效果。
CIP 有效性
對容器或管道進行內部檢查是確定 CIP 有效性的最強大和成本最低的方法之一。 除了一個好的手電筒外,什麼都沒有,很容易看到固體、乾燥的泡沫或殘留的薄膜等不良物。 請務必檢查所有側面、容器頂部、清潔機本身和管道是否有任何清潔不徹底的跡象。 建議在 CIP 的所有位置進行這些目視檢查——預沖洗前、漂洗后、鹼液后洗滌和最終漂洗後。 這樣,您就可以瞭解每個步驟的前後情況,並可以根據需要調整清潔時間。
另一種有效量化 CIP 的方法是使用在線濁度感測器監測回流沖洗液和苛性鹼液。 當濁度下降並保持零值時,可以認為迴路是乾淨的,並且 CIP 步驟可能會推進。 話雖如此,沒有什麼可以取代目視檢查作為 CIP 有效性的最終確認。 無需在每次運行 CIP 時都執行此類檢查。 相反,將此視為應定期安排的系統的檢查點。
我們正處於最後衝刺階段。 每個 CIP 的當前狀態都經過研究並記錄在更新的 PFD 中。 溫度、濃度、清潔作和循環時間都是已知的和經過驗證的。 都很好,對吧? 近。 這項了不起的工作 – 調查、記錄、測試、驗證 – 產生了提供絕對清潔的工藝接觸表面的 CIP,並在更短的時間內完成,使用更少的水和化學品。做得很好! 但如何保證這些成功應用到未來? 歡迎更改管理模式。
管理更改以保持改進
變更管理模式可以採取多種形式,並以數十種方式完成。對於我們的工作,其唯一目的是提供持續的保證,確保我們所學到的知識以及我們在CIP上取得的成功在未來繼續取得成功。
您能想出您或同事觀察到流程偏差的實例嗎?在回顧團隊會議中發生的事情時,是否有人提出了類似這樣的建議,“請讓 Tim 稍微改變一下設定值。那會解決這個問題。然後,那天晚些時候,在一次匆忙的走廊談話中,你要求 Tim 改變這個流程,他做到了。
在此範例中,您對解決方案審查過程有何看法?在提出流程更改之前,對問題的理解程度如何?是否有任何記錄的跡象?這一變化與生產、品質和其他利益相關者的溝通情況如何?
久經考驗的變革管理系統
如果您認為這種流程更改應該得到更好的改進,那麼您是對的。 像這樣的情況每天都在發生。 可以容忍單個實例。 然而,正是這些部分的總和慢慢侵蝕了我們的知識基礎,並允許不確定性重新滲透到我們的過程中。 最常見和最成功的變更管理形式之一是 Plan-Do-Check-Act(PDCA-見圖 6)。 這個久經考驗的系統遵循與我們剛剛用於改進 CIP 的步驟幾乎相同的步驟:
計劃: |
|
做: |
|
檢查: |
|
做: |
|
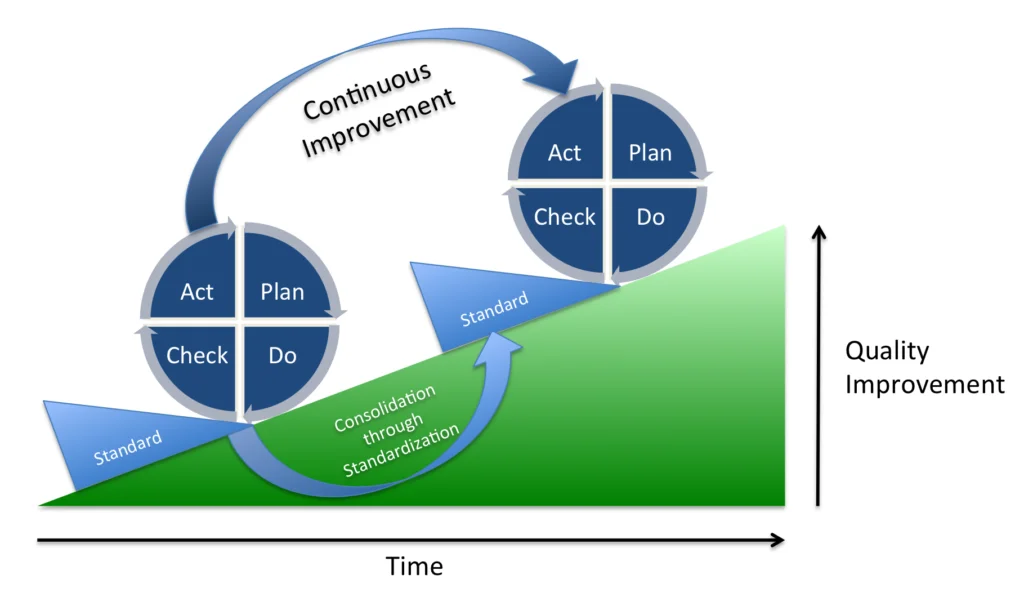
Credit: Johannes Vietze, PDCA Process, CC BY-SA 3.0
與其他解決問題的技術(如精實生產或良率)一樣,行動階段的標準化最終工作將確保這些改進現在被鎖定,並且該過程不會恢復到果去或偏離其當前狀態。
PDCA 是一個強大的過程,是強大的持續改進文化的核心。 要更深入地瞭解 PDCA,請在此處查看美國品質協會的文章。
結束語
你有什麼想法?這是否有助於激勵將 CIP 超越另一項日常任務的願望?您能看到對產品良率和品質的潛在改進嗎?您準備好捲起袖子讓這一切成為現實了嗎?
我的目的是為您提供開始並完成 CIP 改進過程所需的知識。如果您需要支援或需要説明,請知道 LSI 可以在此旅程中為您提供幫助和指導。LSI 傾聽。
關於作者:
Andrew Klosinski 在加入 LSI 之前,他將 14 年的職業生涯奉獻給了啤酒廠。作為一名擁有釀造 IBD 文憑的高級工藝工程師,他説明北美各地的啤酒廠改善運營。他對啤酒行業充滿熱情,看到了運營改進的巨大潛力。Andrew 關注的一個關鍵領域是優化原位清洗 (CIP) 系統,他認為這對公司的成功至關重要。通過改進 CIP 流程,啤酒廠直接影響產品品質、客戶滿意度、可持續性、安全性、員工敬業度和良率。